The recovery of hydrocarbons is basically a volume displacement process. When a volume of hydrocarbon is removed from the reservoir by production, it will be replaced by a volume of some fluid. Energy is expended in this process. Hydrocarbon recovery mechanisms may be divided into two categories:
i) Primary Recovery
ii) Enhanced Recovery
Primary Recovery
Primary recovery is “utilization of the natural energy of the reservoir to cause the hydrocarbon to flow into the wellbore.” Based on this definition, as long as the hydrocarbon flows into the wellbore, this is primary recovery, even if the hydrocarbon must be artificially lifted to the surface by pumps or some other process. There are many sources of this primary recovery energy of which three are dominant:
a) Dissolved Gas Drive ( Solution Gas Drive )
b) Gas-Cap Drive
c) Water Drive
Dissolved Gas Drive
When the reservoir is produced so that gas is permitted to escape from the hydrocarbon liquid in the reservoir, so that two-phase flow (gas and liquid ) occurs from the reservoir\ into the wellbore, the expanding gas will force the oil ahead of the gas into the wellbore. In order to maximize oil recovery, however, for most reservoirs it is desirable to prevent dissolved gas drive, at least until late in the productive life of the reservoir. As the reservoir approaches depletion, the flowing bottomhole pressures may be reduced to as low a value as possible, in order to recover whatever percentage of remaining hydrocarbons might flow into the wellbore, including solution gas from the oil which will
remain in the reservoir (residual oil) at the time the reservoir is abandoned.
Dissolved gas drive can be delayed by injecting water into the water zone beneath the oil, or gas on top of the oil (there creating a gas cap, in order to maintain reservoir fluid pressures above the bubble point pressure.
Gas-Cap Drive
If a gas cap exists above the oil zone, and wells are drilled and perforated in the oil zone and the bottomhole pressures are sufficiently reduced, the expanding gas cap will force the oil into the wells as the gas interface encroaches into the oil zone. In order for gas-cap drive to exist as a primary recovery mechanism, however, the gas cap must exist naturally.
Water Drive
Most hydrocarbon reservoirs will have a water zone beneath the hydrocarbon. This water is tending to encroach into the oil zone. If wells are drilled and perforated in the oil zone, when the wellbore pressure is reduced, oil flow will be initiated into the well as water encroaches into the oil zone forcing the oil towards the producing wells. If this natural encroachment tendency is to exist, natural energy must be present. There are several possible sources of this natural energy. One source is the expansion of the water as a compressible fluid, as reservoir pressures are reduced. As the reservoir pressure is reduced, the expanding water will push the oil in front of it into the producing wells. Water expansion as a compressed liquid produces more oil than oil as a compressed
liquid, not because the compressibility of water is much different to compressibility of oil, but because the total volume of water in the water zone is usually very large when compared to the total volume of oil in the oil zone.
Another source of energy for water drive occurs when the reservoir rock dips upward to the surface where it outcrops. If permeability continuity exists through this rock, as oil is produced from the reservoir, water flows down dip from the surface to replace the oil volume removed. Surface water replenished that water, maintaining a constant hydrostatic pressure on the reservoir fluids.
Secondary Recovery
Secondary recovery is proven technology; indeed, a recent study indicates that 50 percent of all domestic crude oil in the US comes from secondary recovery operations. Water flooding is inherently more efficient than gas displacement in pressure-maintenance projects and is the preferred process where feasible. Some reservoirs, principally those containing heavy oil that flows only with great difficulty, not only provide poor primary recovery but often are not susceptible to waterflooding. Enhanced oil recovery would be especially useful in some of these reservoirs.
Water Flood
Of the historical techniques used for EOR, water flooding has been the most common. This is not water drive. In water drive, water is encroaching into the oil zone from beneath, but in a true water flood, water is injected down injection wells into the oil zone. Ideally, this creates a vertical flood front, pushing the oil in front of the water toward the producing wells. In a water flood, the water injection wells are placed relative to the oil producing wells in some predetermined pattern based on reservoir characteristics and production history. A common pattern for water flooding for large reservoirs which arc basically horizontal reservoirs is the five spot pattern. This five spot pattern is repeated over the reservoir,
Prior to the initiation of a water flood project for a reservoir, various studies will have been made in designing the water flood. These might include model studies in the laboratory, digital and analog computer simulations, and pilot floods may have been run in a portion of the reservoir as a preliminary study, so that an analysis of the water flood plan might be made.
It is desirable to conduct the water flood so as to maximize the sweep efficiency within economic limits relative to production, so that when the water front from the injection wells breaks into the producing wells, a maximum percent of the reservoir volume will have been swept by the flood. Once this water front reaches the producing wells, further hydrocarbon production will be negligible, in that the wells will now produce essentially water. In order to recover further hydrocarbons, a different EOR technique must now be applied as a tertiary (or third) method for recovery.
Whatever the technique used for enhanced recovery, it is desirable that the mobility ratio of driving fluid be less than the mobility ratio for the driven fluid. The mobility ratio is the ratio of the permeability to the flow of the liquid to the dynamic viscosity of that liquid. The oil ratio mobility ratio will be
[ko/mo ] = Oil Mobility Ratio
And, in the case of the water flood, the water mobility ratio of the water will be
[kw/mw ] = Water Mobility Ratio
If the mobility ratio of the driving fluid is greater than the mobility ratio of the driven fluid, the driving fluid will tend to channel or finger through the hydrocarbon, tending to bypass the hydrocarbon in the smaller permeability channels, leaving it behind in the reservoir.
Gas –Cap Injection
In the gas cap drive injection secondary recovery technique, gas is injected into the gas cap above the oil zone, to pressurize the gas cap. In reservoirs where reservoir fluid pressure is higher than the bubble point pressure, a gas cap may be created by gas injection so that the expending gas cap with further gas injection will displace the oil into the producing wells. As previously discussed, gas cap drive or gas cap drive enhancement is often used as a reservoir pressure maintenance technique.
Enhanced Recovery
Processes that inject fluids other than natural gas and water to augment a reservoir’s ability to produce oil have been designated “improved,” “tertiary,” and “enhanced” oil recovery processes. The term used in this assessment is enhanced oil recovery (EOR). According to American Petroleum Institute estimates of original oil in place and ultimate recovery, approximately two-thirds of the oil discovered will remain in an average reservoir after primary and secondary production. This inefficiency of oil recovery processes has long been known and the knowledge has stimulated laboratory and field testing of new processes for more than 50 years.
Early experiments with un-conventional fluids to improve oil recovery involved the use of steam (1920’s) and air for combustion to create heat (1935). Current EOR processes may be divided into four categories:
(a) thermal, (b) miscible, (c)chemical, and (d) other.
Most EOR processes represent essentially untried, high-risk technology. One thermal process has achieved moderately widespread commercialization. The mechanisms of miscible processes are reasonably well understood, but it is still difficult to predict whether they will work and be profitable in any given reservoir. The chemical processes are the most technically complex, but they also could produce the highest recovery efficiencies.
The potential applicability of all EOR processes is limited not only by technological constraints, but by economic, material, and institutional constraints as well.
Thermal Processes
Viscosity, a measure of a liquid’s ability to flow, varies widely among crude oils. Some crudes flow like road tar, others as readily as water. High viscosity makes oil difficult to recover with primary or secondary production methods.
The viscosity of most oils dramatically decreases as temperature increases, and the purpose of all thermal oil-recovery processes is therefore to heat the oil to make it flow or make it easier to drive with injected fluids. An injected fluid may be steam or hot water (steam injection), or air (combustion processes).
Steam Injection.
Steam injection is the most advanced and most widely used EOR process. It has been successfully used in some reservoirs in California since the mid-1960’s. There are two versions of the process: cyclic steam and steam drive. In the first, high-pressure steam or steam and hot water is injected into a well for a period of days or weeks. The injection is stopped and the reservoir is allowed to “soak.” After a few days or weeks, the well is allowed to backflow to the surface. Pressure in the producing well is allowed to decrease and some of the water that condensed from steam during injection or that was injected as hot water then vaporizes and drives heated oil toward the producing well.
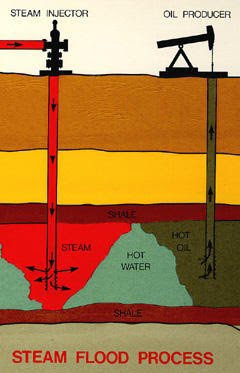
When oil production has declined appreciably, the process is repeated. Because of its cyclic nature, this process is occasionally referred to as the “huff and puff” method. The second method, steam drive or steam flooding, involves continuous injection of steam or steam and hot water in much the same way that water is injected in water flooding. A reservoir or a portion thereof is developed with interlocking patterns of injection and production wells. During this process, a series of zones develop as the fluids move from injection well to producing well. Nearest the injection well is a steam zone, ahead of this is a zone of steam condensate (water), and in front of the condensed water is a band or region of oil being moved by the water. The steam and hot water zone together remove the oil and force it ahead of the water.
Cyclic steam injection is usually attempted in a reservoir before a full-scale steam drive is initiated, partially as a means of determining the technical feasibility of the process for a particular reservoir and partly to improve the efficiency of the subsequent steam drive. A steam drive, where applicable, will recover more oil than cyclic steam injection.
Combustion Processes.
Combustion projects are technologically complex, and difficult to predict and control. Injection of hot air will cause ignition of oil within a reservoir. Although some oil is lost by burning, the hot combustion product gases move ahead of the combustion zone to distill oil and push it toward producing wells. Air is injected through one pattern of wells and oil is produced from another interlocking pattern of wells in a manner similar to waterflooding. This process is referred to as fire flooding, in situ (in place) combustion, or forward combustion. Although originally conceived to apply to very viscous crude oils not susceptible to water flooding, the method is theoretically applicable to a relatively wide range of crude oils.
An important modification of forward combustion is the wet combustion process. Much of the heat generated in forward combustion is left behind the burning front. This heat was used to raise the temperature of the rock to the temperature of the combustion. Some of this heat may be recovered by injection of alternate slugs of water and air. The water is vaporized when it touches the hot formation. The vapor moves through the combustion zone heating the oil ahead of it and assists the production of oil.
Miscible Processes
Miscible processes are those in which an injected fluid dissolves in the oil it contacts, forming a single oil-like liquid that can flow through the reservoir more easily then the original crude. A variety of such processes have been developed using different fluids that can mix with oil, including alcohols, carbon dioxide, petroleum hydrocarbons such as propane or propane-butane mixtures, and petroleum gases rich in ethane, propane, butane, and pentane. The fluid must be carefully selected for each reservoir and type of crude to ensure that the oil and injected fluid will mix. The cost of the injected fluid is quite high in all known processes, and therefore either the process must include a supplementary operation torecover expensive injected fluid, or the injected material must be used sparingly. In this process, a “slug,” which varies from 5 to 50 percent of the reservoir volume, is pushed through the reservoir by gas, water (brine), or chemically treated brine to contact and
displace the mixture of fluid and oil.
Miscible processes involve only moderately complex technology compared with other EOR processes. Although many miscible fluids have been field tested, much remains to be determined about the proper formulation of various chemical systems to effect complete solubility and to maintain this solubility in the reservoir as the solvent slug is pushed through it. Because of the high value of hydrocarbons and chemicals derived from hydrocarbons, it is generally felt that such materials would not make desirable injection fluids under current or future economic conditions. For this reason, attention has turned to C02 as a solvent. Conditions for complete mixing of C02 with crude oil depend on reservoir temperature and pressure and on the chemical nature and density of the oil.
Chemical Processes
Three EOR processes involve the use of chemicals : surfactant/polymer, polymer, and alkaline flooding.
Surfactant/Polymer Flooding.
Surfactant/poIymer flooding, also known as microemulsion flooding or micellar flooding, is the newest and most complex of the EOR processes. While it has a potential for superior oil recovery, few major field tests have been completed or evaluated. Several major tests are now under way to determine its technical and economic feasibility. Surfactant/polymer flooding can be any one of several processes in which detergent-like materials are injected as a slug of fluid to modify the chemical interaction of oil with its surroundings.
These processes emulsify or otherwise dissolve or partly dissolve the oil within the formation. Because of the cost of such agents, the volume of a slug can represent only a small percentage of the reservoir volume. To preserve the integrity of the slug as it moves through the reservoir, it is pushed by water to which a polymer has been added. The chemical composition of a slug and its size must be carefully selected for each reservoir/ crude oil system. Not all parameters for this design process are well understood.
Polymer Flooding.
Polymer flooding is a chemically augmented waterflood in which small concentrations of chemicals, such as polyacrylamides or polysaccharides, are added to injected water to increase the effectiveness of the water in displacing oil.
Alkaline Flooding.
Water solutions of certain chemicals such as sodium hydroxide, sodium silicate, and sodium carbonate are strongly alkaline. These solutions will react with constituents present in some crude oils or present at the rock/crude oil interface to form detergent-like materials which reduce the ability of the formation to retain the oil. The few tests which have been reported are technically encouraging, but the technology is not nearly so well developed as those described previously. Reservoirs not considered for alkaline flooding became candidates for other processes.
Other EOR Processes
Over the years, many processes for improving oil recovery have been developed, a large number of patents have been issued, and a significant number of processes have been field tested. In evaluating a conceptual process, it should be recognized that a single field test or patent represents but a small step toward commercial use on a scale large enough to influence the supply of crude oil. Some known processes have very limited application, for example, if thin coalbeds lay under an oil reservoir this coal could be ignited, the oil above it would be heated, its viscosity would be reduced, and it would be easier to recover. This relationship between oil and coal is rare, however, and the process is not important to total energy production. Another example involves use of electrical energy to fracture an oil-bearing formation and form a carbon track or band between wells. This band would then be used as a highresistance electrical pathway through which electric current would be applied, causing the “resistor” to heat the formation, reduce oil viscosity, and increase oil recovery. The process was conceived over 25 years ago and has been tested sporadically, but does not appear to have significant potential.
A third process in this category is the use of bacteria for recovery of oil. Several variations have been conceived. These include use of bacteria within a reservoir to generate surface-active (detergent-like) materials that would perform much the same function as a surfactant/polymer flood. Although some bacteria are able to with-stand temperatures and pressure found in oil reservoirs, none have been found that will both successfully generate useful modifying chemicals in sufficient amounts and also tolerate the chemical and thermal environments in most reservoirs.It is uncertain whether nutrients to keep them alive could be provided. Further, any strain of bacteria developed would need to be carefully screened for potential environmental hazards.
Recovery Efficiencies
Experience has determined expected ranges of efficiencies of recovery of hydrocarbons by primary and enhanced techniques. These recovery efficiencies are normally expressed in one of two ways:
i.) Percent of Original-Oil-in-Place recovered
ii.) Percent of remaining-Oil-in-Place recovered
The ranges of recovery efficiencies for primary recovery and enhanced may be summarized as follows:
Primary Recovery Efficiencies
Oil (Percent of Original Oil- in- Place)
Dissolved Gas Drive 5% to 30%
Gas-Cap Drive 20% to 40%
Water Drive 35% to 75%
Gas (Percent of Original-Gas-In –Place)
Gas Expansion and Water Drive 90% +
Enhanced Recovery Efficiencies
Oil (Percent of Original- Oil- In- Place)
Water flood (Secondary Recovery) 30% to 40%
CO2 Miscible Flood (Tertiary Recovery) 5% to 10%
Steam Drive (Heavy Oil) 50% to 80%