PROCESSING OF PRODUCED FLUIDS
For oil wells and gas wells, surface processing is intended to reduce the presence of undesirable produced fluids and other materials to a sufficiently low level (percent by volume or percent by weight) to make transportation of the desirable fluids (hydrocarbons) economic to facilities at other locations for further processing and conversion into marketable products.
In the case of crude oil it is normally desirable to reduce water present to a level no greater than two percent of the total volume of the liquids to be transported. In some instances, however, it is necessary to completely remove contaminants during the initial processing. This would be the requirement if hydrogen sulfide (H2S) should be present, in that not only does it create a corrosive environment in the presence of water, but it is also toxic and potentially deadly.
The surface processing system is designed to perform its necessary functions at minimum cost, without endangering personnel or environment, and to retain maximum value of the hydrocarbons while still fulfilling the functions of the processing system. For example, for crude oil in general, the higher the API gravity of oil, the greater its value. Removal of the lighter weight hydrocarbon molecules, such as paraffin series hydrocarbons, reduces the API gravity of the remaining liquids and increases the producing gas-oil ratio with a net loss of hydrocarbon liquid volume. Since the hydrocarbon liquid (crude oil) is normally of greater value than hydrocarbon gas, the processing system is designed to maximize the volume of crude oil available for marketing at as high an API gravity as possible.
The higher the processing temperature to which crude oil is subjected, the lower the API gravity of the resultant crude oil and the lower the volume of crude oil available for transport and sale. Therefore, it is desirable to design the surface processing system to minimize the maximum temperature to which the crude oil is exposed, while still meeting the necessary functions of the system. The design of this system is therefore an optimization process.
Oil Wells
The most commonly produced fluids and materials from oil wells are oil, gas, water (usually salt water), emulsions, and solids. Oil wells are generally classified as either high pressure wells or low pressure wells. If both well classifications are producing into a central gathering system, the high pressure wells will have their production directed to a high pressure manifold, and the low pressure wells will have their production directed to a low pressure manifold.
Fluids produced from high pressure wells normally have a high solution gas-oil ratio, consequently resulting in a higher producing gas-oil ratio. There are several options for this gas, and the option selected will affect specifications for the surface processing equipment. The three most common options for the gas are:
1. Market the gas (or use the gas as a fuel at the location)
2. Re-inject the gas into the hydrocarbon reservoir from which it was produced or into some other reservoir.
3. Flare or vent the gas as waste.
If significant gas is being produced, the third option is not normally permitted be government regulations, in that a natural resource would be destroyed, with adverse effect on the environment. Either of the first two options is more likely to be selected. Therefore, the surface system is designed so that gas produced at the surface is maintained as nearly as possible at the pipeline pressure or the re-injection pressure to minimize cost of recompression of the gas.
Oil Well Surface Processing System
The high pressure well production from the high pressure manifold will initially be directed through stage separators, so that gas is permitted to escape from the oil in stages. From each stage separator, gas, oil, salt water, emulsions and solids may be removed. The solids would tend to settle out due to gravity, but the liquids would essentially flow through each stage of separation, to the free water knockout essentially at atmospheric pressure (or at least at a relatively low pressure as compared to the wellhead pressure) The produced fluid from the low-pressure wells is taken through the same system, with the exception of the multi-stage separation process. The production from the low-pressure well is directed to a low-pressure manifold, from where it flows directly to the free water knockout. From that point to the transportation system, the process system is the same for high-pressure and low-pressure well production.
The free water knockout is essentially a gravity separator with baffles to enhance the separation. The high velocity fluids flow into this separator and upon entry, the flow area is significantly greater, thereby reducing the velocity of flow and enhancing the gravity separation of fluids and other materials into their different densities. Solid particles transported from the reservoir will fall to the bottom of the system, with the fluids stratifying according to density (salt water on bottom, emulsion in the next layer, crude oil in the next layer, with gas rising to the top of the system). The water will contain droplets of oil, the oil droplets of water, and the gas both oil and water droplets, possibly in the form of a mist. As the fluids flow through baffling within the free water knockout, fluid droplets suspended within the other fluids will tend to coalesce, forming larger droplets and enhancing their gravity separation. As the separated fluids exist from the free water knockout, the salt water is removed from the bottom, oil and emulsions are removed from the top of the salt water, and gas is
removed from the top. The water likely contains sufficient oil to prevent its being exhausted to the environment, and may require further processing to remove any remaining oil or other contaminants to a sufficiently low level to permit its disposal overboard, in the case of an offshore operation, into the surface environment, or reinjection into a subsurface formation through a salt water disposal system. The oil, and certainly the emulsion, flows from the free water knockout to an emulsion treater to breakthe emulsion and remove as much additional water as is practical.
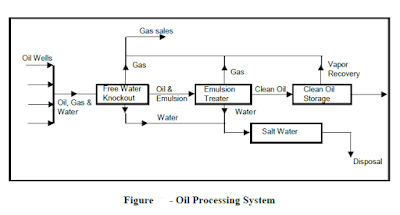
There are several different emulsion treating processes. Historically, one of the most common has been the heater treater, in that increased temperature will break the emulsion. The oil and the emulsion flows from the free water knockout into the heater treater, where it flows down the “down-comer” to the bottom of the heater treater. There it is exposed to the heater, thereby increasing its temperature.
The increased temperature tends to break the emulsion with the heavier water moving downward and the lighter oil upward, through gravity separation. There may be baffling in the system through which the oil passes, further breaking the emulsion. The oil is skimmed from the top of the water and, if the processing system has serve its function, is then transported for storage or to the transportation system (pipeline, offshore tanker, rail cars etc.)
Since the heater treater has increased the temperature of the system, additional gas is formed and is removed from the top of the heater treater, to be combined with the gas obtained from the free water knockout. It is then recompressed for transport or reinjection into the reservoir. The water from the emulsion treater must be transported for disposal.
If hydrogen sulfide (H2S) and/or carbon dioxide (CO2) are present in the produced fluid, they are normally removed from the oil and gas after exiting from the free water knockout, to minimize exposure of downstream processing systems to the corrosive environment which exists when H2S and/or CO2 is present. Dependent upon the volumes of H2S and/or CO2 produced, various removal systems are available. One of the most common is the amine system.
Since the heater treater increases the temperature of the produced fluids, the API gravity as well as oil volume are both reduced, thereby reducing the value of the produced hydrocarbons. Therefore, other emulsion treater systems may be used. Others available include electrostatic emulsion treaters, chemical treatment to break the emulsions, and molecular sieves. The electrostatic treaters takes advantage of the fact that the H2O molecule is an electric dipole so that, when exposed to an electrostatic field there is an attraction for the water molecule, thereby enhancing separation from the hydrocarbon.
The gas is removed from the stage separators, the free water knockout, and the emulsion treater will likely be directed to a dehydrator for further removal of H2O molecules. The dehydration process is the same as that process which will be discussed relative to production from gas wells. Both the crude oil and the hydrocarbon gas leaving the system will be transported for processing into marketable products.
Gas Wells
Production from gas wells may include hydrocarbon gas, carbon dioxide (CO2), hydrogen sulfide (H2S), hydrogen, helium, oxygen, nitrogen, other gases, hydrocarbon liquids and water in the form of droplets or vapor, and suspended solid particles such as sand particles. Solid particle suspension, however, should minimized at the reservoir to reduce the “sand blasting” effect on the production casing and/or tubing, wellhead components, and surface equipment. Surface processing of production from gas wells is usually less complex than for oil wells. From the wellhead, production passes into a gathering system delivering production to the central processing facilities or topside facilities on an offshore gas production platform.
Gas Well Surface Processing System
In normal operations, gas well production flow into a gravity separator, which is basically a large tank. The velocity of the flow from the gathering pipeline decreases significantly upon entering the separator, so that gravity separation occurs. Solid particles and liquid droplets fall to the bottom of the separator, and gases move to the top. If there is sufficient liquid accumulation from gravity separation, the hydrocarbons, usually condensate will float to the top of any water present. Using a baffle system to separate the liquid hydrocarbons from the water, the hydrocarbons will be removed by pipeline to a central gathering location. Water will be removed from the bottom of the separator, and solids will accumulate. The gravity separator tank must occasionally be flushed or backwashed to remove accumulated solids from the bottom of the separator. Gas is taken from the top of the separator. If H2O content and content of other gases is sufficiently low, the hydrocarbon gas is transported to market by pipeline, used as an energy source at the location, or re-injected.
The hydrocarbon gas leaving the gravity separator may contain too much H2O for transport, injection, or use as fuel. If this should be the case, it will pass to the dehydrator for removal of H2O molecules to an acceptably low level. This will usually be a glycol dehydrator, using components such as ethylene glycol, for removal of the H2O molecules from the hydrocarbon gas. The glycol molecule has a greater affinity (attraction) for the H2O molecule than does hydrocarbon. Glycol dehydration is therefore a relatively simple operation.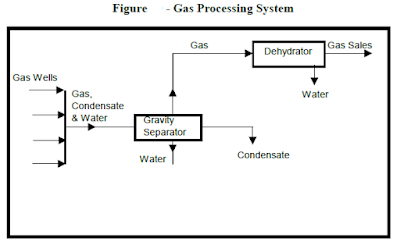
The hydrocarbon gas is passed into the base of a glycol dehydration tower, where it rises, bubbling through trays containing glycol, exposing the hydrocarbon gas to as large a surface area of liquid glycol as is practical. As the hydrocarbon gas bubbles through the glycol, the H2O molecules are attracted to the glycol and are removed from the hydrocarbon gas, with the” dry” gas being removed from the top of the glycol tower. “Dry” glycol (glycol without the presence of H2O molecules) flows on a continuing basis into the top tray of the layered trays in the tower, and flows downward through the tower from one tray to the next, accumulating H2O molecules as the hydrocarbon gas bubbles through the glycol. By the time the glycol reaches the base of the tower, it is now “wet” glycol (glycol with a significant H2O molecular content). This process of removing the H2O molecules from the hydrocarbon gas has not been a chemical process, in that no chemical reactions have occurred. There have been no molecular changes. This “wet” glycol is removed from the base of the dehydration tower.
The H2O molecules are then removed from the glycol as it is prepared for recirculation as “dry” glycol, back into the dehydration tower. Removal of the H2O molecules from the glycol is not complex,, since H2O boils at a lower temperature than does glycol. The “wet” glycol is taken to a temperature higher than the boiling point of H2O, yet lower than the boiling point of glycol, boiling the H2O molecules from the liquid glycol, leaving it “dry”. The “dry” glycol is then re-circulated
back to the glycol dehydration tower.
If hydrogen sulfide H2S and/or carbon dioxide (CO2) should be present in the production from the gas wells, the gas taken from the top of the gravity separator is taken through a process to remove the H2S and/or CO2 before dehydration. Several types of processes are available to remove the H2S and/or CO2, the most common being an amine system as mentioned in the discussion for processing the fluids produced by oil wells. H2S and CO2 molecules have a greater affinity (attraction) for amine molecules than for hydrocarbon molecules, so in a similar fashion to glycol removal of H2O molecules from hydrocarbon gas, the amine removes H2S and CO2 molecules. H2S and CO2 are corrosive in the presence of water; therefore it is desirable to remove them early in the processing system, to minimize exposure of downstream equipment to this corrosive environment.
The hydrocarbon liquid, usually condensate, taken from the bottom of the gravity separator, is transported for storage or used downstream. If production is on or near an offshore platform with an oil pipeline, the condensate may be used to “spike” the crude oil in the pipeline by mixing it with oil. This mixing of the condensate with the oil increases the API Gravity of the crude oil. The hydrocarbon gas exiting from this surface processing system normally requires no further processing.
For oil wells and gas wells, surface processing is intended to reduce the presence of undesirable produced fluids and other materials to a sufficiently low level (percent by volume or percent by weight) to make transportation of the desirable fluids (hydrocarbons) economic to facilities at other locations for further processing and conversion into marketable products.
In the case of crude oil it is normally desirable to reduce water present to a level no greater than two percent of the total volume of the liquids to be transported. In some instances, however, it is necessary to completely remove contaminants during the initial processing. This would be the requirement if hydrogen sulfide (H2S) should be present, in that not only does it create a corrosive environment in the presence of water, but it is also toxic and potentially deadly.
The surface processing system is designed to perform its necessary functions at minimum cost, without endangering personnel or environment, and to retain maximum value of the hydrocarbons while still fulfilling the functions of the processing system. For example, for crude oil in general, the higher the API gravity of oil, the greater its value. Removal of the lighter weight hydrocarbon molecules, such as paraffin series hydrocarbons, reduces the API gravity of the remaining liquids and increases the producing gas-oil ratio with a net loss of hydrocarbon liquid volume. Since the hydrocarbon liquid (crude oil) is normally of greater value than hydrocarbon gas, the processing system is designed to maximize the volume of crude oil available for marketing at as high an API gravity as possible.
The higher the processing temperature to which crude oil is subjected, the lower the API gravity of the resultant crude oil and the lower the volume of crude oil available for transport and sale. Therefore, it is desirable to design the surface processing system to minimize the maximum temperature to which the crude oil is exposed, while still meeting the necessary functions of the system. The design of this system is therefore an optimization process.
Oil Wells
The most commonly produced fluids and materials from oil wells are oil, gas, water (usually salt water), emulsions, and solids. Oil wells are generally classified as either high pressure wells or low pressure wells. If both well classifications are producing into a central gathering system, the high pressure wells will have their production directed to a high pressure manifold, and the low pressure wells will have their production directed to a low pressure manifold.
Fluids produced from high pressure wells normally have a high solution gas-oil ratio, consequently resulting in a higher producing gas-oil ratio. There are several options for this gas, and the option selected will affect specifications for the surface processing equipment. The three most common options for the gas are:
1. Market the gas (or use the gas as a fuel at the location)
2. Re-inject the gas into the hydrocarbon reservoir from which it was produced or into some other reservoir.
3. Flare or vent the gas as waste.
If significant gas is being produced, the third option is not normally permitted be government regulations, in that a natural resource would be destroyed, with adverse effect on the environment. Either of the first two options is more likely to be selected. Therefore, the surface system is designed so that gas produced at the surface is maintained as nearly as possible at the pipeline pressure or the re-injection pressure to minimize cost of recompression of the gas.
Oil Well Surface Processing System
The high pressure well production from the high pressure manifold will initially be directed through stage separators, so that gas is permitted to escape from the oil in stages. From each stage separator, gas, oil, salt water, emulsions and solids may be removed. The solids would tend to settle out due to gravity, but the liquids would essentially flow through each stage of separation, to the free water knockout essentially at atmospheric pressure (or at least at a relatively low pressure as compared to the wellhead pressure) The produced fluid from the low-pressure wells is taken through the same system, with the exception of the multi-stage separation process. The production from the low-pressure well is directed to a low-pressure manifold, from where it flows directly to the free water knockout. From that point to the transportation system, the process system is the same for high-pressure and low-pressure well production.
The free water knockout is essentially a gravity separator with baffles to enhance the separation. The high velocity fluids flow into this separator and upon entry, the flow area is significantly greater, thereby reducing the velocity of flow and enhancing the gravity separation of fluids and other materials into their different densities. Solid particles transported from the reservoir will fall to the bottom of the system, with the fluids stratifying according to density (salt water on bottom, emulsion in the next layer, crude oil in the next layer, with gas rising to the top of the system). The water will contain droplets of oil, the oil droplets of water, and the gas both oil and water droplets, possibly in the form of a mist. As the fluids flow through baffling within the free water knockout, fluid droplets suspended within the other fluids will tend to coalesce, forming larger droplets and enhancing their gravity separation. As the separated fluids exist from the free water knockout, the salt water is removed from the bottom, oil and emulsions are removed from the top of the salt water, and gas is
removed from the top. The water likely contains sufficient oil to prevent its being exhausted to the environment, and may require further processing to remove any remaining oil or other contaminants to a sufficiently low level to permit its disposal overboard, in the case of an offshore operation, into the surface environment, or reinjection into a subsurface formation through a salt water disposal system. The oil, and certainly the emulsion, flows from the free water knockout to an emulsion treater to breakthe emulsion and remove as much additional water as is practical.
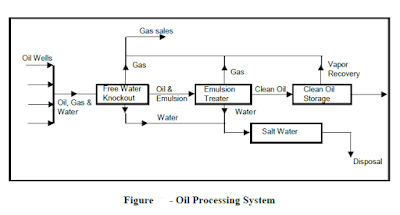
There are several different emulsion treating processes. Historically, one of the most common has been the heater treater, in that increased temperature will break the emulsion. The oil and the emulsion flows from the free water knockout into the heater treater, where it flows down the “down-comer” to the bottom of the heater treater. There it is exposed to the heater, thereby increasing its temperature.
The increased temperature tends to break the emulsion with the heavier water moving downward and the lighter oil upward, through gravity separation. There may be baffling in the system through which the oil passes, further breaking the emulsion. The oil is skimmed from the top of the water and, if the processing system has serve its function, is then transported for storage or to the transportation system (pipeline, offshore tanker, rail cars etc.)
Since the heater treater has increased the temperature of the system, additional gas is formed and is removed from the top of the heater treater, to be combined with the gas obtained from the free water knockout. It is then recompressed for transport or reinjection into the reservoir. The water from the emulsion treater must be transported for disposal.
If hydrogen sulfide (H2S) and/or carbon dioxide (CO2) are present in the produced fluid, they are normally removed from the oil and gas after exiting from the free water knockout, to minimize exposure of downstream processing systems to the corrosive environment which exists when H2S and/or CO2 is present. Dependent upon the volumes of H2S and/or CO2 produced, various removal systems are available. One of the most common is the amine system.
Since the heater treater increases the temperature of the produced fluids, the API gravity as well as oil volume are both reduced, thereby reducing the value of the produced hydrocarbons. Therefore, other emulsion treater systems may be used. Others available include electrostatic emulsion treaters, chemical treatment to break the emulsions, and molecular sieves. The electrostatic treaters takes advantage of the fact that the H2O molecule is an electric dipole so that, when exposed to an electrostatic field there is an attraction for the water molecule, thereby enhancing separation from the hydrocarbon.
The gas is removed from the stage separators, the free water knockout, and the emulsion treater will likely be directed to a dehydrator for further removal of H2O molecules. The dehydration process is the same as that process which will be discussed relative to production from gas wells. Both the crude oil and the hydrocarbon gas leaving the system will be transported for processing into marketable products.
Gas Wells
Production from gas wells may include hydrocarbon gas, carbon dioxide (CO2), hydrogen sulfide (H2S), hydrogen, helium, oxygen, nitrogen, other gases, hydrocarbon liquids and water in the form of droplets or vapor, and suspended solid particles such as sand particles. Solid particle suspension, however, should minimized at the reservoir to reduce the “sand blasting” effect on the production casing and/or tubing, wellhead components, and surface equipment. Surface processing of production from gas wells is usually less complex than for oil wells. From the wellhead, production passes into a gathering system delivering production to the central processing facilities or topside facilities on an offshore gas production platform.
Gas Well Surface Processing System
In normal operations, gas well production flow into a gravity separator, which is basically a large tank. The velocity of the flow from the gathering pipeline decreases significantly upon entering the separator, so that gravity separation occurs. Solid particles and liquid droplets fall to the bottom of the separator, and gases move to the top. If there is sufficient liquid accumulation from gravity separation, the hydrocarbons, usually condensate will float to the top of any water present. Using a baffle system to separate the liquid hydrocarbons from the water, the hydrocarbons will be removed by pipeline to a central gathering location. Water will be removed from the bottom of the separator, and solids will accumulate. The gravity separator tank must occasionally be flushed or backwashed to remove accumulated solids from the bottom of the separator. Gas is taken from the top of the separator. If H2O content and content of other gases is sufficiently low, the hydrocarbon gas is transported to market by pipeline, used as an energy source at the location, or re-injected.
The hydrocarbon gas leaving the gravity separator may contain too much H2O for transport, injection, or use as fuel. If this should be the case, it will pass to the dehydrator for removal of H2O molecules to an acceptably low level. This will usually be a glycol dehydrator, using components such as ethylene glycol, for removal of the H2O molecules from the hydrocarbon gas. The glycol molecule has a greater affinity (attraction) for the H2O molecule than does hydrocarbon. Glycol dehydration is therefore a relatively simple operation.
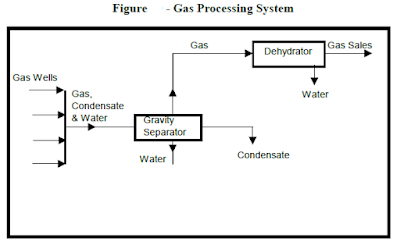
The hydrocarbon gas is passed into the base of a glycol dehydration tower, where it rises, bubbling through trays containing glycol, exposing the hydrocarbon gas to as large a surface area of liquid glycol as is practical. As the hydrocarbon gas bubbles through the glycol, the H2O molecules are attracted to the glycol and are removed from the hydrocarbon gas, with the” dry” gas being removed from the top of the glycol tower. “Dry” glycol (glycol without the presence of H2O molecules) flows on a continuing basis into the top tray of the layered trays in the tower, and flows downward through the tower from one tray to the next, accumulating H2O molecules as the hydrocarbon gas bubbles through the glycol. By the time the glycol reaches the base of the tower, it is now “wet” glycol (glycol with a significant H2O molecular content). This process of removing the H2O molecules from the hydrocarbon gas has not been a chemical process, in that no chemical reactions have occurred. There have been no molecular changes. This “wet” glycol is removed from the base of the dehydration tower.
The H2O molecules are then removed from the glycol as it is prepared for recirculation as “dry” glycol, back into the dehydration tower. Removal of the H2O molecules from the glycol is not complex,, since H2O boils at a lower temperature than does glycol. The “wet” glycol is taken to a temperature higher than the boiling point of H2O, yet lower than the boiling point of glycol, boiling the H2O molecules from the liquid glycol, leaving it “dry”. The “dry” glycol is then re-circulated
back to the glycol dehydration tower.
If hydrogen sulfide H2S and/or carbon dioxide (CO2) should be present in the production from the gas wells, the gas taken from the top of the gravity separator is taken through a process to remove the H2S and/or CO2 before dehydration. Several types of processes are available to remove the H2S and/or CO2, the most common being an amine system as mentioned in the discussion for processing the fluids produced by oil wells. H2S and CO2 molecules have a greater affinity (attraction) for amine molecules than for hydrocarbon molecules, so in a similar fashion to glycol removal of H2O molecules from hydrocarbon gas, the amine removes H2S and CO2 molecules. H2S and CO2 are corrosive in the presence of water; therefore it is desirable to remove them early in the processing system, to minimize exposure of downstream equipment to this corrosive environment.
The hydrocarbon liquid, usually condensate, taken from the bottom of the gravity separator, is transported for storage or used downstream. If production is on or near an offshore platform with an oil pipeline, the condensate may be used to “spike” the crude oil in the pipeline by mixing it with oil. This mixing of the condensate with the oil increases the API Gravity of the crude oil. The hydrocarbon gas exiting from this surface processing system normally requires no further processing.