Motor Orientation/Control
All directional wells require steering during initial kick offs, correction
runs, sidetracks, and re-drills. Once the desired direction in which the tool
should be faced is determined, the next step is to actually face the tool in
that direction in order to drill the predetermined course.
For the Mach 1/AD motor, a cartridge data transmission (CDT) system has
been developed that allows orientation of the motor in a particular
direction, while still allowing drilling with drillstring rotation. This CDT
system uses a special heavy duty steering tool which provides continuous
surface readout of the drift angle and azimuth, as well as toolface
orientation while drilling ahead.
A “hard wire” from the steering tool, through the drillstring to the surface,
relays the information to computerized surface equipment. Data
transmitted from the steering tool is updated and converted instantly to
information which can be used to make any necessary corrections to the
motor.
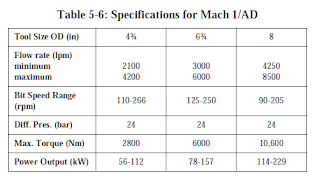
All directional wells require steering during initial kick offs, correction
runs, sidetracks, and re-drills. Once the desired direction in which the tool
should be faced is determined, the next step is to actually face the tool in
that direction in order to drill the predetermined course.
For the Mach 1/AD motor, a cartridge data transmission (CDT) system has
been developed that allows orientation of the motor in a particular
direction, while still allowing drilling with drillstring rotation. This CDT
system uses a special heavy duty steering tool which provides continuous
surface readout of the drift angle and azimuth, as well as toolface
orientation while drilling ahead.
A “hard wire” from the steering tool, through the drillstring to the surface,
relays the information to computerized surface equipment. Data
transmitted from the steering tool is updated and converted instantly to
information which can be used to make any necessary corrections to the
motor.
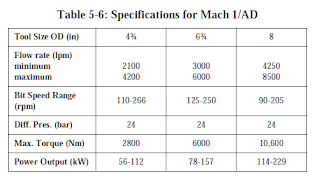