Connecting rod assemblies
Since the rotor is spiral shaped, it does not rotate concentrically, rather it
traces a back and forth motion. This motion must be converted to a
concentric motion to be transmitted to the bit via the drive sub. This is
achieved by a connecting rod assembly. There are several types.
Universal-joint
U-joint assemblies (Figure 5-22a) have been utilized by the industry and
are still used in most positive displacement motors. The assembly consists
of two universal joints, each grease filled, and sealed with oil-resistant
reinforced rubber sleeves to protect them from drill fluid contamination. A
drawback of the U-joint assembly is the lack of sufficient strength for
higher torque applications, such as those encountered with recent
generations of high torque PDM’s, particularly when used with PDC bits.
This inherent weakness is a result of the manufacturing process whereby
the U-joint is “flame-cut” rather than machined.
Flex rod
A recent development in connecting rod assembly technology has been the
utilization of flexible steel or titanium “flex rods” (Figure 5-22b). While
flex rods are limited by the degree of allowable lateral bending, they have
the advantage of low maintenance, since they do not require lubricants or
rubber sleeves. Flex rods are now standard on most smaller Navi-Drills.
One recent approach has been to mount the flex rod inside the hollow rotor
of a short, high torque steerable PDM, rather than connecting it to the
bottom of the rotor. By connecting a long flex rod to the inside of the top
end of the rotor and extending it through the rotor, to connect to the top of
the drive sub assembly, the overall rate of bend is decreased due to its
increased length.
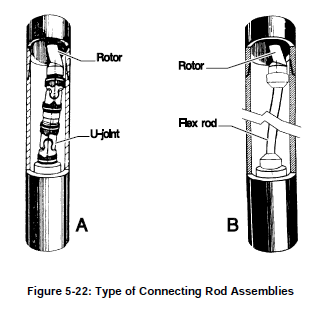
Since the rotor is spiral shaped, it does not rotate concentrically, rather it
traces a back and forth motion. This motion must be converted to a
concentric motion to be transmitted to the bit via the drive sub. This is
achieved by a connecting rod assembly. There are several types.
Universal-joint
U-joint assemblies (Figure 5-22a) have been utilized by the industry and
are still used in most positive displacement motors. The assembly consists
of two universal joints, each grease filled, and sealed with oil-resistant
reinforced rubber sleeves to protect them from drill fluid contamination. A
drawback of the U-joint assembly is the lack of sufficient strength for
higher torque applications, such as those encountered with recent
generations of high torque PDM’s, particularly when used with PDC bits.
This inherent weakness is a result of the manufacturing process whereby
the U-joint is “flame-cut” rather than machined.
Flex rod
A recent development in connecting rod assembly technology has been the
utilization of flexible steel or titanium “flex rods” (Figure 5-22b). While
flex rods are limited by the degree of allowable lateral bending, they have
the advantage of low maintenance, since they do not require lubricants or
rubber sleeves. Flex rods are now standard on most smaller Navi-Drills.
One recent approach has been to mount the flex rod inside the hollow rotor
of a short, high torque steerable PDM, rather than connecting it to the
bottom of the rotor. By connecting a long flex rod to the inside of the top
end of the rotor and extending it through the rotor, to connect to the top of
the drive sub assembly, the overall rate of bend is decreased due to its
increased length.
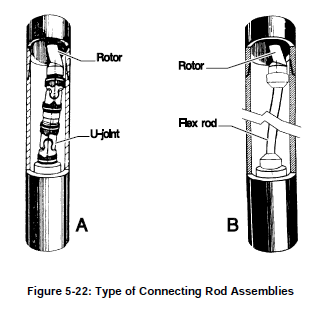