Bearing Section
A typical positive displacement motor utilizes three sets of bearings
attached to a drive shaft. There are two sets of radial bearings (“upper” and
“lower”) with one set of axial thrust bearings.
The axial thrust bearing section supports the on and off bottom loading and
hydraulic thrust. It consists of a series of ball bearings stacked one on top
of the other, each set being contained in its own race (groove). The number
of these bearings will vary, depending on the size of the tool.
The upper and lower radial bearings are lined with tungsten carbide inserts.
These bearings support the concentrically rotating drive shaft against
lateral loads. The inherent design of the upper radial bearing limits the
amount of fluid flow diverted to cool and lubricate the bearing package.
This diversion of flow is typically 2 - 10%, depending on motor and bit
pressure drop. The major portion of the drilling fluid is collected by ports
in the drive shaft and exits through the bit. In some motors, diamond
bearings are used, which need up to 20% of the flow to be diverted,
depending upon conditions. Figure 5-23 illustrates typical bearing sections
found in PDMs.
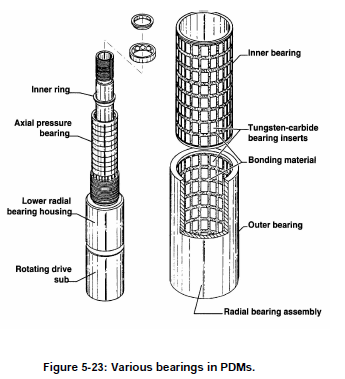
A typical positive displacement motor utilizes three sets of bearings
attached to a drive shaft. There are two sets of radial bearings (“upper” and
“lower”) with one set of axial thrust bearings.
The axial thrust bearing section supports the on and off bottom loading and
hydraulic thrust. It consists of a series of ball bearings stacked one on top
of the other, each set being contained in its own race (groove). The number
of these bearings will vary, depending on the size of the tool.
The upper and lower radial bearings are lined with tungsten carbide inserts.
These bearings support the concentrically rotating drive shaft against
lateral loads. The inherent design of the upper radial bearing limits the
amount of fluid flow diverted to cool and lubricate the bearing package.
This diversion of flow is typically 2 - 10%, depending on motor and bit
pressure drop. The major portion of the drilling fluid is collected by ports
in the drive shaft and exits through the bit. In some motors, diamond
bearings are used, which need up to 20% of the flow to be diverted,
depending upon conditions. Figure 5-23 illustrates typical bearing sections
found in PDMs.
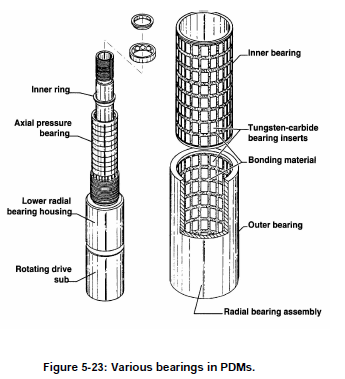